The goal of this study is to investigate the effectiveness of Composite Metal Foam (CMF) armors against 0.50 caliber ballistic threats. A hard armor was manufactured using a sandwich panel construction consisting of a ceramic faceplate, a CMF core, and a thin aluminum back plate. The hard armor system was tested against 0.50 caliber (12.7 × 99 mm) ball and armor piercing (AP) rounds. The CMF armors were tested with a variety of areal densities at impact velocities between 500 and 885 m/s.
The armors stopped the threats at speeds up to 819 m/s without penetration. The CMF layer was found to absorb 73–76% and 69–79% of the kinetic energy of the ball and AP round respectively. When compared to rolled homogeneous steel armor (RHA), the CMF hard armors, in their current unoptimized condition, have a mass efficiency ratio of approximately 2.1.
The CMF armor offers a much needed weight savings without sacrificing protection. Finite element analysis was completed using ANSYS/AUTODYN Explicit Dynamics solver to study the material interactions and impact. The results are shown to be in good agreement with the experimental findings.
The armor of a combat vehicle can affect its viability and use in the field. Lighter vehicles are more maneuverable but tend to have less protection, while heavy armor vehicles, meant to face large caliber threats, are slow and take longer to mobilize into position. The next generation of vehicle hard armors must be lightweight, cost effective, and perform well to an array of ballistic and blast threats [1]. New armors for land vehicles, boats and aircrafts can be used to create more versatile and dependable military vehicles with a higher level of protection while maintaining their maneuverability and stealth. These ideal armor systems must have a balance of high hardness, high strength, and low density. In order to achieve this, a layered system consisting of a ceramic face plate with a composite or metal backing is widely used. Composite armors excel at stopping threats with reduced spalling, but hard armor systems consisting of hardened steel and high strength aluminum alloys are the focus for the newest advancements in vehicle armors to defeat high caliber threats.
Typical hard armor systems use a ceramic faceplate backed by a ductile metal such as steel, aluminum, or titanium. The ceramic layer in the armors is used to blunt, fracture, or rotate the core of the projectile allowing the metallic backplate to absorb the residual energy of the bullet through plastic deformation. Ceramic faceplates are desirable for their low density and high hardness. In recent studies, ceramics such as aluminum oxide (Al2O3), silicon carbide (SiC), and boron carbide (B4C) have been effectively used as armor faceplates. Other works have studied the use of metal matrix composites that pair the hardness of dispersed ceramic particles with the ductility of metals to achieve a similar effect. Researchers are also testing various high strength aluminum and steel alloys that require larger thicknesses to wear away and stop the impending rounds.
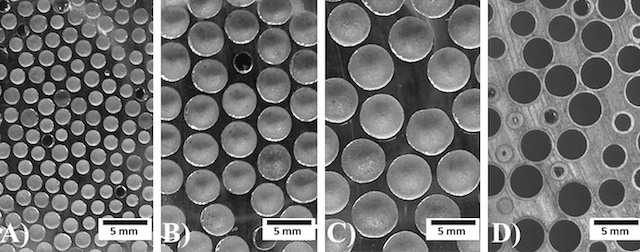
This work studies the use of composite metal foam (CMF) as an intermediary layer between a ceramic faceplate and a thin metal backing to create an efficient and lightweight hard armor solution. Stainless steel composite metal foam (S-S CMF) is a light weight metal foam with a density comparable to aluminum. It is known for its high energy absorption capabilities under compression due to its large strain plateau at high stress. Moreover, prior studies indicate that CMF’s energy absorption capabilities under high strain rate conditions, such as ballistic and blast loading is further strengthened. The CMF layer can improve the energy absorption of an armor while decreasing the armor’s total weight allowing for increased fuel efficiency and overall cost effectiveness of the vehicle. CMF can be made with a variety of metals, but for consistency and brevity S-S CMF will be referred to as CMF throughout the rest of this work.
Initial testing of CMF hard armor systems facing 7.62 × 51 mm ball and 7.62 × 63 mm armor piercing rounds (AP) has previously been reported. The preliminary data showed promising results using CMF hard armors to effectively defeat both ball and AP threats. This study builds on the prior work and explores the use of CMF hard armors to defeat larger caliber ballistic threats such as the 12.7 × 99 mm ball and AP rounds, also known as the 0.50 caliber ball and AP. A finite element analysis of the AP ballistic impact was used to validate the experimental findings and build upon the current model for CMF armor systems.
Composite Metal Foam Materials & Processing
The CMF panels were manufactured by sintering together stainless steel hollow spheres and stainless steel powder using a powder metallurgy technique developed in previous works. The spheres were manufactured by Hollomet GmbH in Dresden, German and consist of a 2 mm diameter with a 100 µm thick wall. The metal powder used was 316L stainless steel purchased from North American Höganäs. The CMF panels were manufactured in 25 × 25 cm and 30 × 30 cm sizes with a variety of thicknesses.
Composite metal foam vs 12.7 × 99 mm ball results
Table 4 lists the results of the ballistic testing with the samples organized by the type of threat, areal density and impact velocity. Out of the three panels tested against 12.7 × 99 mm ball rounds, one had a series of nine 10 × 10 cm ceramic faceplates arranged over the surface to cover the 30x30 cm CMF panel. The other two samples had a single 30 × 30 cm ceramic faceplate and are used to compare the performance between the two arrangements. Images of the front and back of B1 and B2 CMF.
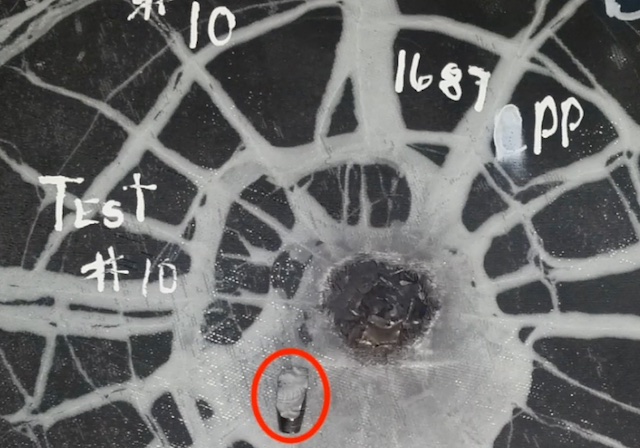
S-S CMF panels were manufactured and paired with a ceramic faceplate and aluminum backplate. The layered hard armors were tested against 12.7 × 99 mm ball and AP rounds at a range of impact velocities. The mild steel cores of the ball rounds penetrated one of the three samples but reveal the benefits of using multiple tiles over a single ceramic faceplate to limit the spread of damage. The hardened steel core of the AP rounds penetrated deep into the ceramic faceplate, compressing the CMF layer...
Source: sciencedirect.com
Comments
Post a Comment